①残業時間を減らしたい
こんな悩みを抱えています・・・
働き方改革やワークライフバランス。
世に浸透してきているこういった取り組みは分かる。分かってはいるんだけど、なかなか残業を減らせない。
従業員も疲れているし、モチベーションも上がらない。
こんな状況で改善なんてとてもじゃないけど言えない。負のスパイラルだ・・・どうしよう。
大企業・中小企業問わずこのようなお悩みを抱えている企業様は少なくありません。
毎月平均75時間残業、しかしそうなると法律に触れてしまうので強制的に休みを取ってもらう。
でも休むとドンドン仕事が溜まる。他の人に負荷がかかって他の人の残業が増えてしまう。
特に「この人じゃないと出来ない」という仕事がある場合には更に深刻になってしまいます。
さて、困った。どうやって解決しよう。
そんな企業様からのご依頼を解決した事例をご紹介しましょう。
オーソドックスな業務改善
ヒアリング、現場視察にて大きな課題をまず洗い出しました。
しかし、顕在化している課題は実は本質の課題の数歩手前である場合が多いので大きな課題(と認識されている)点を現場張り付きやフレームワークなどで徹底的に掘り下げていきます。
その後、根っこの課題が抽出できたところで対策を立案していきます。
そうして出た対策案に対して評価していきます。
ここでいう評価とは、実施するのに必要な時間・実施するのに必要な費用・実施した場合に見込まれる効果・実施後、効果が現れるまでの時間などをそれぞれ定義付けした上で点数を付けます。
評価した数字の高い対策案から優先的に実施していき、効果を見つつ実行した改善に対して修正を加えていくといった流れです。
非常にオーソドックス且つ「普通じゃないか」という流れですが、やはり基本は重要です。
私が入ったからこそ出来た事は?
一点目は、第三者目線だからこそ固定概念のないフラットな視点で本質的な課題を発見出来る事です。
これは私でなくても言えるメリットです。「外部に依頼する強み」とも言えるでしょう。
これは非常に重要な視点で、固定概念に凝り固まってしまうと本当の根っこの問題は出てこないのはどんな企業でも同じ事が言えます。
二点目は、現場の肯定感と納得感を持った改善が出来る事です。
私は現場作業員として工場で勤務経験もあり、現場改善を現場視点で10年近く行ってきました。
よって、理想論や机上の空論ではなく現場従業員の方々の思いにも寄り添った改善を実施出来ます。
だからこそ、スピード感があり従業員の方々が自ら率先して実施する改善を行う事が出来ます。これはプロジェクトが終わった後にも大きな効果を発揮すると評価を頂いております。
三点目は、経営者と現場の距離が近づく事です。
経営者が思っている、現場に望んでいる事を現場へ分かりやすく現場の方々が腹落ちするように落とし込み、現場が思っている事を体型的・具体的に経営者に伝えます。
これにより、お互いの間にあった「何故」が払拭出来るばかりか信頼しあえる関係性構築にも一役買います。
これは、現場と経営両方を経験して身についた定性的な「感性」や「思い」を重要視してきたから出来る事なのでしょう。
どんな効果が出るの?
残業時間削減による効果
現場従業員30人×残業時間1.5時間/日の削減×20日×12ヶ月
=10,800時間/年 の残業削減を達成
1時間あたりのチャージを3,000円で換算。
=3,240万円/年の効果!
勿論、生産キャパシティー(生産出来る量)は変わっていないベースの比較です。
定性的な効果
- 業務改善による効果を実感した従業員の方々が自ら改善提案するようになった
- 報告の際や提案の際に数字を用いた定量的な説明をするようになった
- 発言が「どうやったら出来るか」というスタンスに変わった
- 何故この問題が起こっているかという視点をあらゆる事に対して持つようになった
- 経営者と現場の心の距離感が近づくことにより会社全体の雰囲気がよくなった
などなどの嬉しいお声を頂いております。
②外に出るお金を減らしたい
こんな悩みを抱えています・・・
生産は確かに忙しいけど、負荷状況によっては時間が余っている時もある。それなのに部品や材料をかなり外注してしまっている。
確かに外注する事で助かっている部分は多いが、出来る物は社内で作っていきたい。
でも、どの部品をどのようにして中に取り込むか。それが問題だ。
利益が出ておらず、現場のキャパシティーも逼迫している状態でない場合内製化は検討しなければならない重要なポイントです。
しかしながら「昔からの付き合い」などの関係性等において内製化に踏み切れない。
または「社内で作る余力はない」という反発により内製化に踏み切れない。
こういったケースは非常に多いものです。自社の経営が立ち行かないのが最悪の状況だが、付き合いや今までの恩義というのも確かに重要視しなければならない大きなポイントですよね。
では一体どのように解決すればいいのでしょうか。
内製化の計画と進捗管理
色々な面からプロジェクトを進める事が重要です。内製化を進めるのであれば原則「出来る時もあれば出来ない時もある」という状況はNGです。無駄な在庫を抱えなければならない上にコントロールも容易ではないからです。
内製化に踏み切るアイテムを決めたら当該アイテムはコンスタントに作れるような工程設計が重要。そして内製効果がどの程度かにもよりますが出来れば増員なしで内製出来る仕組みにしたいものです。
よって、生産効率を高めつつ内製効果のあるアイテムを選出します。
最も重要なポイントの一つが品質です。
外注事と変わらぬ、品質が上がるような製品にしていく必要があります。
生産効率、場所、人。そういった様々な要素を加味した上でどのアイテムを内製化していくのかを検討する必要があるのです。
また、それらのプロセスが決まった後のスケジュールに対する進捗管理も必須です。
どのタイミングで外注発注を止めて内製し始めるかなどあらゆる調整が必要です。外注先への交渉も、お付き合いを断絶するような形でなく、きちんとその背景と意図を説明する真摯な対応が肝要となってくるのです。
私が入ったからこそ出来た事は?
一点目は、様々な部署や様々な事の調整や必要な行動を明確にする事が確実且つ迅速に出来ます。
これは、ノウハウを持っているからこそお伝え出来るポイントです。
過去に内製化に取り組んだ事のない企業様においては特にこの調整や「しなくてはならない事」のリストアップに苦労します。
そういった要素を一つ一つ修正しながら少しづつ前へ進めていく中で状況が変わり、内製化が止まってしまうなんて事もよくある事です。だからこそ、確実に迅速に進めるというポイントが重要となるのです。
二点目、内製化すべきアイテムの効果的な選定が出来る事です。
ここで言う効果的というのは、希望的観測で「出来るだろう」という選定ではなく現場の会社の状況を見極めつつ、内製効果が高く且つ品質面においても要求を満たすアイテムの選定が出来るという事です。
勿論チャレンジは重要ですが、その中において数字を紐づけていくという事です。
どんな効果が出るの?
内製化による効果
前述した通り、内製化を実施する際には業務改善等により増員なし、生産キャパシティーは維持出来るようにして行っていく為、単純に内製化しているアイテムの年間購入金額が純粋な利益になります。
例>
アイテムA=年間400万円、アイテムB=年間1,200万円
だと、年間効果は純粋に1,600万円になります。
定性的な効果
- 当たり前に購入していた部品に対し、コストという意識が芽生える
- 当たり前を変革させる事で「変化」させる事の効果を知り、改善への取り組み方が変わる
- 部署間でのコミュニケーションが増える
- スケジュール管理の重要性を知り、実践する事が出来るようになる
という効果が出ているようです。
③多能工化や、人員の効果的な配置を行いたい
こんな悩みを抱えています・・・
「この人がいないと仕事が回らない」という仕事がある。だから誰かに覚えてもらいたいんだけど、他の生産工程も忙しいから中々覚える時間がない・・・。
現場作業をしている方を何名か現場から抜いて、管理業務に回ってもらいたいんだけど現場が忙しくてどうにもならない。新たに人を雇うしかないかなぁ。
生産キャパシティーを落とさず、現場作業従事者の絶対数を削減するという取り組みは企業にとって必要な動きです。勿論、ここで捻出する事が出来た人材は管理者になって頂いたり間接部門で新たな部署に参加いただく事でさらに会社として成長する事が重要な次のステップとなります。
多能工化を進める上でも有効なのですが、どのように進めるのかといった点においてはお困りの企業様が多いのが現実です。
人材を捻出すると同時に次の取り組みを明確にする
人材を捻出する為の基本的な流れ、進め方は前項・前々項でも記載した生産効率向上を以てして行います。
その上で「何故、なんの目的で人材を捻出するのか」を明確にしましょう。
例えば多能工化を進める事が目的であれば、どのような範囲において多能工化していかなければならないのかなどを見えるようにする為、スキルマップや対応可能工程がわかる人別の多能工マップを作ってもいいでしょう。
そうして圧倒的に対応出来る人が少ない生産工程を重点的にカバーしていくなど、感覚的ではなく体型的に行っていく事が重要です。
また、違う部署に移動する際には引き継ぎ期間などもあらかじめスケジューリングして進捗度合いを管理していく事も必要です。
業務改善も平行して行う必要がある為、大きな変革となる取り組みには違いありませんので計画が誰から見てもわかるよう、そして現状がどのような状態にあるかなどを視覚化する事で効率的に進める事が出来ます。
私が入ったからこそ出来た事は?
一点目、業務改善と平行して取り組む事が出来る。
人員の配置転換や多能工を進める施策については、無理をして推し進めるといった手段をとる企業様も少なくありません。しかし、そのような進め方では従業員の方々からの反発の声が上がりモチベーションが下がったり、上手く施策が進まなかったりと結果として効率が悪い状況に陥ってしまいます。
業務改善により生産効率を上げ、多能工や配置転換しやすい状況を作り、現実的且つ効果的な教育スケジュールを立てる事が出来ます。
二点目は、可視化により必要な行動が見える、進捗がわかるように出来る事です。
どの工程を強化しなくてはならないか、現状誰がどのようなスキルを持っているのか、誰がどのようなスケジュールでどこの工程習熟しなくてはならないのか。
これらを誰の目にもわかるようにマップ化し進捗管理する事が出来ます。
どんな効果が出るの?
増員せずに人員不足の解消が出来る
生産効率向上を中心とした業務改善を行う事により、製造現場のキャパシティーを維持して必要な人員を削減したり生産できる絶対量をあげる事ができます。
そこで捻出出来た貴重な人材を負荷が高くて困っている部署へ移動させるなどして、新たな人材を雇用する事なく確保する事が可能です。
既に会社の仕組みを知っている人材を異動させる事が出来るため教育期間なども比較的短期で済むのも大きなメリットです。
多能工を進める事で現場力強化を図れる
特定の人しか出来ない作業や仕事というのはどこの企業でも意外と多く存在します。
そのような状況は会社にとって非常に危険であり、特定の人しか出来ない仕事が重要な事であればあるほどそのリスクは高まります。
仕事を休まなければならない場合や長期離脱する事などがあれば会社が立ち行かなくなってしまうからです。
そんな状況を回避する為にも多能工化を進める事は重要なのです。
多能工を進める事でそういった状況を回避する事が出来るばかりか、特定のタイミングで負荷がたった場合にも人員を回し、効率よく対応する事が可能となります。
生産現場の総合力が上がるという効果があるのです。
定性的な効果
- 今自分に与えられている仕事意外に学ぶ事が出来る為、モチベーション向上につながる。
- マップを作成する事で工程毎の状況や人のスキルなどが可視化出来る。
- スキルマップなどを作成する事で人事評価制度などと繋げる事が出来る
生産効率を向上させる=会社の利益につながる
生産効率を向上させたいと考えるのは、目的があります。
- 製造原価を下げたい
- 利益を上げたい
- 残業時間を下げたい
- 人員の削減や多能工化を進めたい
- 生産量を上げたい
生産効率を向上させるのは、業務負荷が高い時ばかりではありません。
受注量などが減り、業務負荷が下がった場合も生産効率を向上する事で会社の利益確保に大きな効果を発揮するのです。
企業はいつも何かの課題を抱えています。それは、「現状の問題」や「成長する為の課題」であったり様々です。
業務改善はどんな時でも企業にとって必要な取り組みなのです。
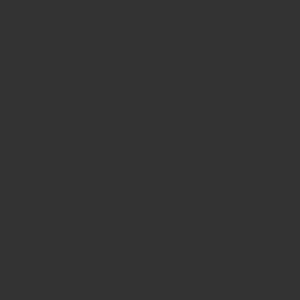
業務改善は基本的にこの図のように進んでいきますが、不慣れ且つ試行錯誤しながらでは膨大な時間を要してしまいます。
社内で業務改善を進める中で投資対効果については重要視すると思います。
幾ら投資し、その投資で得られる効果がどの程度か。このバランスや回収年数に応じて投資判断をすると思います。ここでよく抜け落ちるのは「その検討や導入に係る人員の労働時間とその費用」です。
外部に発注する際にはその費用を投資として認識するにもかかわらず、社内の従業員の方が行う際にはその費用は勘定には入れない。だからこそ、とかく長い時間を費やしてしまったり効果が薄かったりしてもさほど気に留めないという状況が生まれ、改善の文化が根付かない場合があるのです。
例えば改善に5人×月に10時間投じたとすれば50時間。50時間あればあなたの会社の商品が何個作れますか?
そして、その利益は幾らになりますか?
従業員の時間を使うというのはそういう事です。そこも投資である事を忘れてはならないのです。
本項のタイトルにもある通りですが、
業務改善をすると会社の利益は上がります。
しかし、利益をあげるためには「投資額を減らし、効果を最大化する」事がとても大きな要素となります。
そして、投資額という観点の中で従業員の時間を使うことも投資であるという観点を持たなければ効果を最大化することは出来ません。
業務改善を知り・従業員が進んで実行出来るようになる5sトレーニングとは?
5sという言葉は特に製造業の方であればよく知っているのではないでしょうか。
しかしながら5sの本当の価値や進め方を知っている企業は意外と少ないのです。
多くの企業では、5sを単なる清掃活動と位置付けておりその効果を最大化出来ていません。
適切な5sが出来ている職場では、業務効率が上がり、従業員のモチベーションや改善に対する意欲が高い。
そして自信に満ちて会社が良くなる為の方法を自ら考えるようになるのです。
嘘だと思いますか?しかし、5sが出来ている企業では挨拶一つとっても5sが出来ていない企業と比較すると雲泥の差が出ます。
ご自身の会社・職場で「もっと意識を高めて欲しい」や「モチベーションを上げて業務に取り組んで欲しい」と思うことはありませんか?
そういったお悩みを解決する一つの手段として私がご提供する5sトレーニングがあります。
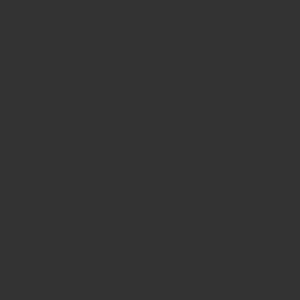
この5sトレーニングが他と最も違う点は、実践を伴うトレーニングであるという点です。
座学や講習、セミナーなどで5sに関する知識教育をする企業様は多いですが、知識を蓄えるだけでは現場は変わりません。「これで5sについてはわかりましたね、ではやっておいてください」では進まない事の方が多いのです。
私の5sトレーニングでは、まず適切な知識を身近な物で例えながらディスカッションを通して何をすべきか具体的にイメージ出来るようになります。
次に、一つの現場のさらに限定した場所で5sを実践します。
この実践が非常に重要です。何から手をつけてどのように進めなければならないのかと言う点は「聞いただけ」と「やってみた」で大きく理解度が変わります。
実践を通してどのように進めるかと結果としてどう変わったかを経験する事で次のステップでも自ら考えて5sに取り組む事が出来るのです。
その後に、評価する場を儲けます。ここでは、「出来た事」に対する賛辞と「もっとこうしたら更によくなる」というポイントを中心に変化を遂げた現場に対して数名厳選してコメントします。
最後にアフターフォロー。
これは基本線現場の従業員のかたへは内緒でとある一定期間後にご訪問させていただきます。
その際に現場の5sが維持出来ているか、更に進化しているかなどをフォローアップし、更に次のステップを明確にします。
ここまでを1つのパッケージとしてご提供しているのが私の5sトレーニングです。
効果は座学だけのセミナーとは雲泥の差。従業員の意識が変わると共に「変化」を体験し、効果を実感した従業員の方のモチベーションが上がる事は間違いありません。
さらにはこの5sトレーニングを実施する事で業務改善の基礎的な部分がわかるようになる為、社内の業務改善も劇的に進むようになります。
5sトレーニングを受講→業務改善の実行という流れで私をご利用下さった企業では大きな効果を出して、1年経たずして投資を効果が上回っている企業が殆どです。
本5sトレーニングは半日で完了する為、生産に対する影響も極めて少ないというのも高評価頂いているところです。
実際の5sが体験出来、従業員の意識が変わり、モチベーションが上がる。業務改善のスピードや取り組む姿勢が劇的に変わるこの5sトレーニングは全国どこでも、
50,000円+税+交通費
でご提供させて頂いております。
トレーニング後に、5s以外の様々なお悩みを伺う無料診断もセットとなっていますので是非一度体感してみては如何でしょうか。
皆様からのお問い合わせを楽しみにお待ちしております!
お問い合わせ
各種お問い合わせ方法は以下の通りです!
いつでもお気兼ねなくお問い合わせくださいませ!お待ちしております!
LINEでのお問い合わせ
LINEでもお問い合わせを受け付けております。
以下のバナーをクリックしていただくか、QRコードを読み取って友達登録をお願いします!
その後、メッセージよりお問い合わせいただければ必ず1営業日以内にご返信させていただきます!
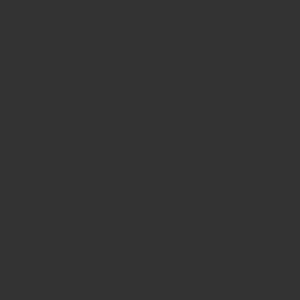
電話・メールでのお問い合わせ
電話・メールでのお問い合わせもお待ちしております。
電話の場合、もし取り込み中でご対応出来ない場合でも必ず折り返しさせていただきますのでお気兼ねなくご連絡くださいませ!
いつでもお気軽にお問い合わせください。050-8888-7887受付時間 9:00-17:00 [ 土・日・祝日除く ]
お問い合わせはこちら t-osawa@leo-makoto.com