事例①某社製造ライン生産効率30%向上プロジェクト
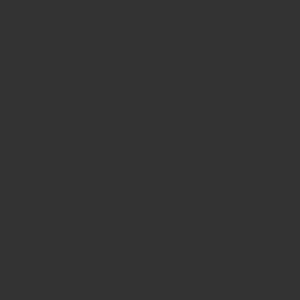
A社は製造ラインでものづくりを行う所謂流れ作業で日々生産を行っている工場でした。
同一ラインで様々な種類の製品を流す必要があった為、各工程における負荷の大小が非常に顕著で、Xという製品の時は8工程目がライン停止を起こしZという製品の時は10工程目がライン停止を起こしてしまうというアンバランスな生産ライン構造となっていました。
また、生産ラインの出口に検査工程が設置してあり、且つ検査項目が膨大であったため検査工程ではいつもラインが停止してしまいスムーズな生産が出来ずにいるといった課題をお持ちでした。
そこで、お声がけ頂いたのですが依頼内容は『生産能力30%向上』といった事でした。
私は条件として、プロジェクトチームを設置頂く事だけを提示しこの依頼を受け現場の確認作業を行いました。
課題は山積み。問題点はどこにあるか
まず現状を正確に把握する事が全ての原点。と言う事で各工程における製品毎のデータを計測し表にまとめる作業と現場従業員の方々に対するヒアリングを始めました。
それと同時に全体感を把握する為非常にマクロな視点で特性要因図を作成するなどし、どこにどのような原因があるかという点においてあらゆる切り口から確認を行っていったのです。
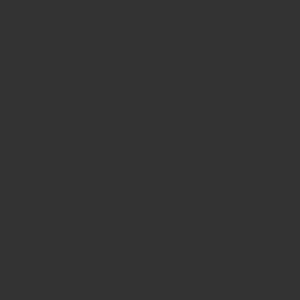
これは、どこの企業様においても起こっている事の一つですが、目の前で顕在化している『事象』を問題点として認識している場合が極めて多い。
『これが問題だ』と決めつけてしまい、本当の問題が霞んでしまうという危険な状況になる事を避けるためにも、客観的な視点を持つという事が非常に大事になってきます。
解決案と実行
問題の抽出を進める際にはプロジェクトメンバーへしっかりレクチャーを行いながら考え方や進め方を答えに導きながら先導します。
現状と問題が把握出来たら次は解決案を出していきます。様々な解決案が出てきますがここで重要なのは優先順位付け。
実行する事の絞り込みとその評価方法です。
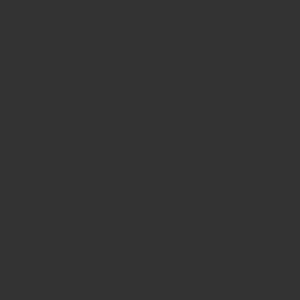
納期・効果・コストそして効果が出るまでの時間という観点で評価を実施しました。
それぞれの項目に明確な判断基準を付与し、その合計点を以て実行する案の選定と優先順位をつけていきました。
このプロジェクトにおいては生産工程の平準化や生産日程の調整、一部設備投資や班毎の組織構築・変更。リリーフマンの導入や検査内容の絞り込みと検査場所の再検討、レイアウト変更など100以上出た改善案のうちから10個程度集中的に実施する項目を決めて実行していきました。
私の信条として『必ず効果を出す』事としていますので実行フェーズも一緒に作業着で実施したりします。
効果は出たがあと少し
結果、ラインはスムーズに流れるようになり、生産効率は25%程度向上しました。
しかしながら目標までは届いていません。よって、残り5%を達成する為に更なる改善案の抽出を実施し、実行。
効果確認をして最終的には35%の生産効率向上を達成しました。
追加で価値を
それに加え、私は関わらせて頂いた先で必ず5sを実施する事としています。※お客様から『絶対にやらないでくれ』と言われない限り。
いい仕事は整った環境から。
5sを実施する事の意味と価値、そしてどのように進めていくのかという点において一つずつ丁寧に教え、実行していきました。
プロジェクトが終わるころには辺りに落ちていたゴミや部品などはどこにもなくなり、指定席化された場所に必ず物が置かれている 『探さなくていい職場』。
そして、日々の清掃とそれに伴う異常の早期発見など。
職場全体が明るく、活気に満ちた向上に変貌を遂げました。
一言
現場は生き物です。そして従業員の方々は会社にとって財産です。
ムダな事をしている、ムダを省こうなどとよく口にされる方がいらっしゃいますが、多くの方々はそれがムダである事に気づいていません。
自分の仕事がムダだといわれる事は気持ちのいいことではありません。
私は、これを『改善ポイント』や『もったいない所』という表現をします。
やはり言い方や伝わり方で相手のやる気や取り組む姿勢というのは変わり、それはとても重要なポイントだと思うのです。
私はそういった面において、重要視し且つ確実に効果が出るように導く点においては誰にも負けるつもりはありません。
会社として、笑顔が増える環境を創り出す。増やす。これが私の力になります。
実績紹介は今後も定期的にふやしていきますので是非ごらんになっていただければと思います!
無料相談、トライアル期間もご用意しております!
当社では、まず初回のご挨拶とヒアリングは無料(広島県以外では交通費のみ頂戴いたします)で行っており、その後トライアル期間というものをご用意しております。
ご安心してなんなりとお申し付けくださいませ!
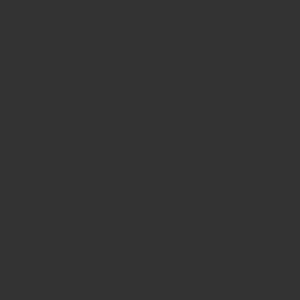
連絡先
メール・電話でのご連絡はこちら
0823-32-0070