こんにちは。広島県の改善コンサルタント株式会社LEO-Makoto大澤です!
製造工場のみならずどこの職場においても”5s”というのは改善における基本の”き”と言っていい程重要な事です。
しかしながら実際にこれを実行するのは存外難しいものです。
5sと聞くと多くの方が抱くイメージは『きれいにする』や『見栄えをよくする』というような部分ではないでしょうか。
では一体何のためにきれいにしたり見栄えをよくするのでしょうか。
昨今この5sという言葉が先行し、”5sが目的”となっているケースをよくみかけます 。
しかしながら5sというのは手段であって目的にはなり得ないのではないか。
私はそう考えるのです。
本記事ではその理由と私なりの見解、経験してきた5sという物に対してのアプローチを記載していく事と致しますので、お付き合いくださいますよう宜しくお願い致します!
5sについて
5sとは??
- 整理 (Seiri)
- 整頓 (Seiton)
- 清掃 (Seisou)
- 清潔 (Seiketsu)
- 躾 (Shitsuke)
この5つの”S”を5sと呼びます。会社によって幾つかの”S”を追加して6sや7sというケースもあります。
では具体的にこれら5つの”S”は何をどうする事を指しているのか。特別難しい事ではなく、多かれ少なかれ必ず企業において実行している事なのですが、企業として『5sに取り組む』というのは5sの重要さを理解し、それが安全・品質・生産効率及びマーケティングにまでも重要な効果をもたらす事を知っているという姿勢が伺えます。
しかしながらこれらを遂行したいが具体的に何が必要でどういった施策を進めるべきか、分からないという企業も多くみられます。
私は工場、営業所、オフィスと過去に5sについて幾らか実行及びコーチングに携わってきました。
本記事では私の拙い経験について記載させて頂きます。少しでも皆様のお役に立てれば幸いですのでご一読下さいますよう宜しくお願い致します。
整理 Seiri
皆様は『整理』に対してどうお考えでしょうか。
『整理』というのは不要な物を処分する事を言います。ただし、それぞれにおいて『不要な物』というカテゴリーに分類する事自体が難しい場合が多いのも事実です。
昔私が5sを推進していた頃に実施した物に”3秒判別”というのがあります。
この3秒という数字に根拠は特になかったのですが、結果としてこの方法が少なからず役に立ったので今も使用する事は多いです。
方法は至ってシンプルで、必要か必要でないかを3秒で判断するだけというものです。
この方法で『これは要る物?』と聞くと基本的に以下の4つに分類されます。
- 必要
- 不要
- 必要といえば必要だが絶対必要ではない
- 不要だがもったいない
1は残す、2は捨てる。
3のような物は存外沢山あり、整理出来ない一番の要因はこういった『必要な時がある』という物です。
要は『現場になくてもいいが必要である物』。こういった物は倉庫や、共用の工具置き場といった保管場所へ一次保管。
そして4『いらないけどもったいないなぁ』といった物。これは処分です。
おもしろいくらい前述した4つに分類されるはずです。
そしてこの分類は自職場で実施すると4の分類項目である『不要だがもったいない』という物が何かしらの理由を付けて残りがちなので、客観的な目を入れると更に徹底した整理の実行が可能となります。
整頓 Seiton
整理をして、必要な物のみが手元に残りました。では次は『整頓』です。
ここでいう『整頓』とは探さない環境を作る事を指します。
では探さない環境を作るというのは具体的に何をするか。私は以下の点を実行する事としています。
- サイズや種類毎に置き場を分ける
- 現場に応じた表示方法で誰がみても分かり易い表示を施す
- 斜めがいいか、垂直がいいか『取り易さよりも戻しやすさ』を考慮して置き方を工夫する
この3点だけです。ただし、この中で3点目の赤字部分を特に重要視しています。
取り易さも勿論重要ですが、それよりも重要なのは戻しやすいかどうかです。その工具や物を”取る”という行為は作業に必要なので極端な話、取りにくくてもなんとか取り出します。(勿論取り易いように置くのは当然ですが)
”戻しにくい”置き場であれば多くの場合、決められた場所に戻さずにその辺に置いてしまいます。
つまり、整頓を継続する仕組みを作れていないのです。
探さない環境を作り、且つそれを継続させる仕組みを作るというのがこのキモの部分になるのです。
清掃 Seisou
清掃。これはキレイな状態を保った上で異常に気付く為の点検をする事です。
様々な現場における生産設備やその他設備、オフィスにおける様々な機器。形ある物は必ず壊れます。
そして多くの場合、壊れた後に気付くのです。
埃まみれで油が漏れている事にすら気付く事なく生産を行い、案の定生産設備が破損して止む無く修理完了まで2日間工場の操業を停めざるを得ない工場。この会社の損害は考えるまでもなく甚大です。
では、この工場で毎日清掃を行っていたとしましょう。
恐らく油漏れに気付き、工場を停める事なく修理を完結させてこのような甚大な被害は出なかったのではないでしょうか。
これは実際に私が携わらせて頂いた事例を省略して書いた物ですが、このような事例は沢山あるのです。
そしてこれは生産のみならず品質や安全にも大きく関わってくる事となり、決して軽んじてはならない重要な『経営におけるリスクヘッジ』の一つでもあるのです。
清潔 Seiketsu
清潔とは整理整頓清掃された状態を維持する事を言います。
先ほど、整理整頓された状態を維持し日頃から清掃されていれば自然と清潔が保たれる訳ですね。
簡単に言いますが『維持する』というのは非常に難しい事だというのは経営者の方や管理監督者の方であれば痛いほど分かるのではないかと思います。
この次の項目で出てくる『躾』と管理監督者が徹底して5sを理解して継続させる強い意思が必要となります。
躾 Shitsuke
整理、整頓、清掃、清潔を習慣づける事がここでいう躾の部分になります。
特にこれまで5sに対しての取り組みが積極的でない企業において5sを『当たり前』に変化させていくのは非常に難しい事です。
言い続けて、出来ていない事一つに対しても必ず守らせていくという徹底した姿勢が必要になります。
その中で前提になるのは、会社としての取り組みで整理をして整頓を進め、清掃を出来る時間を確実に取り、清潔を維持する環境をきっちり整備してあげる事です。
それらを用意して躾のフェーズに移行する事で5sの土台が整う訳です。
5sを継続出来た事でしっかり現場を褒める体制を経営者がとってみるのもいいでしょう。
例えば、5sに対して各職場単位で取り組みを評価して優良職場には何か報酬や表彰を実施する、等です。
まとめ
如何でしたか?5sに対しての取り組みは単純なようでその実維持継続という面で相当なパワーと労力を使う事になります。
経営者、管理監督者が本気で取り組み、全員がその重要さを理解して初めてスタートラインに立つのです。
私が過去関わらせて頂いた企業様は5sに取り組みたい気持ちがありながら中々徹底出来ずにいました。が、それでは5sは維持継続の面で悉く失敗に終わっていったのです。
全員が同じ方向を向き、徹底してこれを貫く。
そしてそれを会社としての当たり前にして初めて5sが根付くのです。
5sを実施する事で得られる事として、清掃しながら点検をする事でより早く異常を察知できる事。
品質、安全面の向上。
お客様が工場に来られた際に『こんな5sが進んだ工場で作られた製品ならいい物に違いない』と思っていただける環境づくり。
あらゆる面で5sはプラスに働きます。
こういった5sに対する取り組み。是非実行してみては如何でしょうか。もし私に出来る事があればサポートさせて頂きますのでお気軽にご連絡下さいませ。
2020年9月28日追記
当社では、補助金申請のサポートもさせて頂いております。
5s活動や業務改善活動におけるサポートに関して、小規模事業者持続化補助金等制度を有効活用する事によって事業者様にとって負担を軽減しながら様々な活動が出来るサポートも可能ですので是非一度弊社の無料相談からご連絡頂ければと思います。
- 導入前の不安を解消!MARUNAGE(バックオフィスBPO)に関するQ&A
- 補助金の基本を押さえよう!補助対象経費を徹底解説!
- 提出しないと補助金返還!?事業化状況報告とは?
- 補助金申請をオンラインで簡単に!jGrants(Jグランツ)の使い方と活用方法
- 中小企業必見!GビズIDについて徹底解説
関連記事
お問い合わせはこちら
いつでもお気軽にお問い合わせください。050-8888-7887受付時間 9:00-17:00 [ 土・日・祝日除く ]
お問い合わせはこちら t-osawa@leo-makoto.comLINEでのお問い合わせはこちら
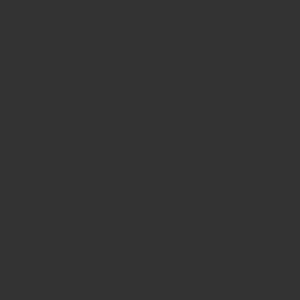