過去に様々な業界で業務改善を行わせて頂きましたが、特に多いのが「製造業」での経験です。
と言う事で本日はこれから改善に着手する製造業と何度か挑戦したがうまく行かなかった製造業の皆様へ向けた記事となります。
最後までお付き合い頂ければと思いますのでどうぞよろしくお願い致します。
製造業における現場改善の始め方
Step1:目的と目標を明確に伝える
製造現場は日々のルーティンである「生産」に追われています。
本日の生産数はどれくらいで、どの程度のペースで作業を行う必要があるのか。
今日は〇〇社向けの商品があるから負荷が高い、など特に生産管理などが適切に機能していない場合にはこの難易度や朝の調整に時間がかかるという会社も非常に多いのです。
そんな忙しい日々の中で「改善活動」を織り込むとなるとまず最初に「時間がない」という声が挙がるのではないでしょうか。
それもそのはず。この段階において「業務改善」は突然課された追加の仕事。
従業員の皆様や現場管理者の方々からしてみれば「なんでやるのか」「なんで今なのか」といった声が挙がるのは必然なのです。
経営者側からしてみると「当たり前の事」でも従業員の皆様にとっては「当たり前ではない」事。
このギャップを埋めるのは容易ではありません。
何故なら、持っている情報量もひっ迫感も会社情勢も、従業員個々人の単位ではさほど「自分事」ではないからです。
どれだけ「やれ」と言った所でそのギャップは埋まりません。そしてもっと言うとこれを強烈なトップダウンで無理やり実施させても継続しないという状況が生まれてしまう場合もあるのです。
よってまずは従業員一人一人にしっかりと改善を行う目的を知ってもらう必要があります。そしてもっと言えば目標についても明確に示す事で方向性が定まると言えるでしょう。
事例A(悪い例)
生産能力を上げる為に、業務改善を行ってください。あと汚いから現場の5sもちゃんとしなさい。
えっ、業務改善?確かに改善しなきゃいけないとこは沢山あるけど、何をどうすんの?
5sって、掃除すればいいんだっけ?
じゃぁよろしく。生産も遅らせないようにね。うまく考えてやってください。残業は今まで通りね。
わわわ、生産も忙しいのに新しい仕事?しかも残業も出来ないってどうするんだよ。
適当に簡単な事でもやったふりするかぁ、、
非常に極端な例ではありますが、まぁ言ってしまえばこのような指示を出して進捗は確認せず、出来ていない事に対して怒るという会社も少なくありません。
何のためにやるのか、そしてその時使う単語などは誰もが分かる言葉を使うなど、経営者様の「当たり前」と従業員様の「当たり前」はまるで違うのです。
5sという単語一つとっても、本当に5sの事を教育しており従業員様一人一人がきちんと理解している会社では社内の共用語として使えても、そうでない会社では「ただの掃除」と理解されている場合もあります。
こういった教育に関しても非常に重要な要素なのです。
事例B(良い例)
いつもお疲れ様です。受注が増えて忙しくなってきましたので生産量を上げる為に業務改善を行いたいと思います。
現状1日当たり100個の生産を120個に上げる為に現場毎で「こうすれば出来る」という意見を来週月曜日までに出して頂けますか?
100個から120個なら、新しい設備を入れるとかじゃなくて現場での改善でなんとかなりそうだな。普段から「こうしたい」と思ってた事もあるし、提案してみるか!
後は、定期的に開催している5sの教育に関してですが、現場でよくできていると思います。もう一段階レベルを上げる為にも特に「整理」と「整頓」の部分をもう一度見直す事で効率アップさせる活動も積極的に取り入れてください。
確かに!まずは5sで整理整頓をしてから身の回りの「探す」手間や「仕分ける」手間などを省いた方がよさそうだ。
そのうえで更に効率化しなければならない所を見つけ出していこう!
具体的な目的と目標がある事で、従業員様が「どの程度の改善規模か」を考える事が出来ます。
且つ、5sの教育も行き届いている為「5sの本質」をしっかり分かっていますね。
更にはきちんと状況を期限つきで確認するなど進捗管理もできている事から地に足付いた改善が始まる事でしょう。
このように、指示を出す時に目的と目標を明確に伝える。そしてその項目一つ一つに期限を設けて進捗を確認する。
社内で伝わる共用語で認識のズレがない状況を創り出す。
簡単そうに見えて非常に難しいことが出来ているようです。
Step2:簡単な事から始める
業務改善を行うという時にいきなり大きな改善から着手する会社も多いのです。
ノウハウがない内からいきなり「生産効率を30%上げるぞ!」などの目標を打ち立てても中々進まないばかりか、途中で頓挫して後の改善に対しても「どうせまたすぐ諦めるよ」といった風潮が出来てしまうのです。
業務改善にこれから取り組む会社にとってまず必要なのは「成功体験」です。
なのでノウハウを持っていない内に業務改善を始めるのであれば確実な成功を手にする為の比較的簡単且つ効果が分かり易い事から始める事をお勧めします。
具体的な例で言うとやはり5sがあがります。
しかし、注意してほしいのは5sを単なる「掃除」と位置づけていたのでは改善に繋がらないという事。
しっかりと5sの教育を行い、「なんのためにやるか」「どのようにやるか」を明確にして始めましょう。
そして、しっかりと成果が出た場合にはちゃんと褒めてあげてください。
また、実施している間は必ずその様子を気に掛けてあげてください。
こういった小さなことが従業員様のモチベーションに繋がり、次のレベルの改善に進む為の重要な足掛かりとなるのです。
Step3:体制を整える
ここで言う体制とは、主に以下の事を言います。
- チーム
- 時間
- 仕組み
ひとつづつ見ていきましょう。
1.チーム
業務改善はチームで行う方が成功する確率が上がります。
話ながら一緒に目標に向かえる事と、もし誰かが突発案件によって改善に関われない場合でも周囲の方々で進める事が出来るからです。
重要な事は「走り出した物を止めない」事。一度でも止まってしまうともう一度始める際には多少苦労する事になってしまいます。
2.時間
可能な限り決まった「時間」を設けてあげてください。
例えば水曜日の定時から1時間は改善の時間などです。そう決めてあげる事で改善に取り組む頻度や取り組む姿勢が均一になり不平不満が生まれにくい事と、改善の文化定着にも一役買います。
3.仕組み
改善を行っていない人に罰を与えるような形ではなく、改善を行い成果が出たチームに対して何かしらプラスになる制度のような物を設けてあげる事で改善は加速度的に進みます。
会社のメリットと併せて個人またはチームでのメリットを付加してあげるのです。
会社の為にした事が自分たちに還元される仕組みというのを構築している会社では改善の取り組み方が全く違います。
まずここで紹介した3つの体制を整えていく事で改善文化の定着や改善に取り組む姿勢、モチベーションが上がる事は経験上間違いありません。
是非参考にして頂き、改善着手に役立ててみてください。
最後に
本記事でご紹介させて頂いた3ステップは何れもすぐに取り組める内容となっています。
企業が成長する上で改善は欠かせないものであり、確実に推し進めなければならない重要な活動です。
弊社ではこういった改善活動が定着する仕組みや従業員様が確実に改善に取り組める体制の構築。
そして、改善の考え方や5sの意味などをレクチャーしていきながら業務改善を遂行する事を得意としています。
ノウハウ+教育=企業の改善力向上。
これは私が十数年積み上げてきた改善のキャリアにおいて、必須といえる取り組みだと常々実感してきたところです。
是非参考にして頂き、企業様の改善にお役に立てて頂ければ幸いでございます。
お問い合わせ
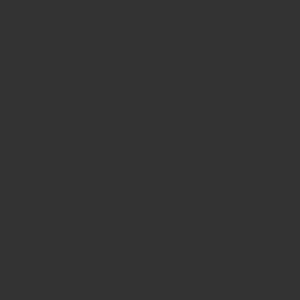
いつでもお気軽にお問い合わせください。050-8888-7887受付時間 9:00-17:00 [ 土・日・祝日除く ]
お問い合わせはこちら t-osawa@leo-makoto.com